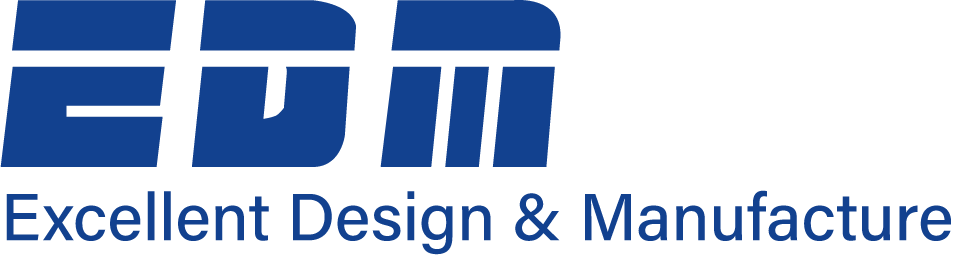
EDM one piece, forged, bonnetless steel globe valves are designed and manufactured in accordance with ASME B16.34.This includes high pressure drop, steam blow down, steam injection, fast acting isolation, 6000 psi(414bar) gas and super heated steam at 1100°F(593°C) . Valves are available in sizes NPS 1/2" to 4". It is with pride that we offer to the user this outstanding,long-lasting, high performance valve for high pressure and tough applications.
A wide range of body materials are available including A105, F11, F22, F91, F92, F316, F316H and F321 etc.
End Connections are available with Socket Weld, Butt Weld, Screw and Flange.
Special service applications such as NACE Mr0175 can also be provided.
■One-piece,forged,bonnetless globe valves eliminate the potential for body-to-bonnet joint leakage,and not require cut or disassemble the bonnet for servicing.
■65° inclined body reduces pressure drop compared with T-type.
■Splined bushing guides the stem allows quick and easy maintenance by removing all working parts at one time.
■The non-rotating stem hardened and polished to reduce operating torque.
■Linearly instead of helical movement of the non-rotating stem reduces the total friction area between the packing and stem.
■Packing chamber burnished and combination graphite rings individually pre-stressed for tight seal.
■Two-piece gland ensures gland and packing self-aligning.
■Stellite disc,seat and backseat provide excellent long service life even in severe services.
■Fully guided disc auusres seat and disc precise alignment in spite of side thrust caused by high velocity flow,and prevents stem from scoring and galling,and provides longer disc seal and body life.
■Double orifice design protects seating faces because of the erosive flow energy dissipates through disc.
■Two flat shots design at the internal bottom of the disc prevent the disc from rotating,so avoid high-speed rotating disc and seat contact,damage to disc and seat.
■Backseat bevel on the stem,not on the disc,meet specifications API-602.
■Large clearance between stem and disc allows disc to move freely.
■Dust cover and sleeve protect stem threads from dirt,dust and sand.
■Fully enclosed stem driving lubrication system with two needle roller bearings ensures low operating torque.
■Upper stem position indicates if valve is open or closed.
■Optional live-loading packing,disc springs keep packing tight for long periods of time without maintenance.
■Stop,regulating,and stop check discs are available.
■Handwheel is ruggede and knobbed to make sure the grip even wearing gloves.
■Optional handwheel colors are available.
The function of a boiler or turbine drain valve is to allow the discharge of condensed steam out of the pipework or system.
The condensed steam ( condensate ) will be at a temperature slightly below the boiling point or saturation temperature corresponding to the pressure of the steam in the system.
In modern supercritical or ultra supercritical power plants where the live steam pressure can be in the order of 25 – 30MPa, this means that the condensate could be at a temperature in excess of 300℃.
The condensate is normally drained to a low pressure system, this means that at the moment the drain valve is opened the condensate pressure is reduced to a level below its saturation pressure, and it flashes into superheated steam.
The flashing of the condensate into steam causes a large increase in volume which means that there must be a high velocity flow through the valve in order to drain the condensate.
High velocity flashing steam can cause a number of problems for a valve that is fundamentally designed for isolation service.
The flashing steam can cause wire drawing or erosion of the sealing surfaces of the valve. Once the sealing surfaces are damaged the valve will start to leak when it is in the closed position.
The high velocity will also mean turbulent flow which can cause vibration in the valve and adjoining pipework.
This vibration can cause damage to the valve including wear of the seating surface which again would mean a leaking valve in the closed position.
A standard globe Isolation valve is often selected for drain applications due to its relatively low cost, however standard globe Isolation valves are not designed for high pressure drop service, and they normally wear out very quickly requiring expensive repair or replacement.
For the end user it is less expensive in the long term to install a high quality valve that is specifically designed for drain service.
The EDM Globe Drain valve has two stages of pressure reduction. The first stage is cage with several holes sized and machined to ensure that most of the pressure drop through the valve takes place through the cage, rather than the valve seat. This design ensures that the possibility of wire drawing damage to the valve seat is minimized.
The valve stem and disc, seat , and cage are all removable with the valve in line, and can be easily replaced. This means the valve does not have to be cut out of line to be repaired, and avoids the need to replace the complete valve in the event of disc or seat damage.
The valve body is designed to ensure that the centre of gravity is as close to the pipe axis as possible. This is to ensure that valve and pipe vibration caused by the highly turbulent flow is minimized.